by Julie | May 19, 2016 | Consulting, Employee Training, Management, Process Improvement
Tips to Enhance Employee Involvement in Process Improvement
I enjoy trying new recipes but if you know me at all, I’m not very good at following instructions. So, the first time I try a recipe, I will try to follow the instructions and for the most part, use the specified ingredients. If a recipe proves to be worth trying again, I will begin analyzing the instructions in order to find a more efficient way to prepare the dish.
I am sure that the creator of the recipe came up with the process based on the skills and equipment that she had, but, my kitchen set-up is different and as a result, I’m sure I can find a more efficient way to achieve the same results.
The Job Methods program within Training Within Industry has a similar goal but on a much larger scale. This program was developed to teach employees to understand and improve their work and to sell their improvement ideas to their supervisors, peers and upper management. The goal is to give plant personnel the tools they need in order to produce more products in less time with the same level of quality while utilizing the available resources.
If you believe that your plant has opportunities to enhance employee involvement in your process improvement initiatives, I would make the following suggestions:
- State the organizational goals and how improving the process of how things are done will help achieve those goals. Make sure these goals are congruent with the workforce goals, i.e. increased profitability.
- Give employees the freedom to question how things are done. Don’t allow the phrase “but we have always done it that way” to be used. Perhaps set-up a friendly fine for the person who expresses that sentiment.
- When looking at ways to improve a process, utilize a Job Methods Breakdown sheet in order to capture all the steps in the process and then question every step. Ask Why? What? Where? When? Who? How? as you work through each of the steps.
- Provide employees a method for making suggestions for process improvements. I have often heard employees say that they have made suggestions but no one ever accepts them. But, in order for a process improvement idea to be made, it needs to be well thought out and presented in a setting where constructive feedback can be made and received.
- Make sure employees receive recognition for their ideas. The more recognition they receive; the more ideas they will generate.
Employee involvement in continuous improvement activities is an important key to the success of manufacturing companies. But, without the proper training and support, employees may end up feeling disconnected from these activities. Effective communication, robust training and an open and supportive workplace will go a long way towards achieving your productivity goals.
For more practical tips for manufacturing professionals to attract, train and retain your hourly workforce, go to www.keyprocessinnovations.com.
by Julie | May 17, 2016 | Consulting, Efficiency, Employee Training, Management
Training Supervisors on Conflict Resolution
Dealing with conflict is an important part of a healthy work environment. And making sure people have the skills to resolve those issues was so important that Job Relations Training was included as one of the four programs within Training Within Industry. Donald Dinero in his book “Training Within Industry” said Job Relations Training “gives supervisors an easy method to use on a daily basis to inform their decisions and make their jobs easier.”
The program includes a 4 step method for handling conflict. As I read through the 4 steps (Get the Facts, Weigh and Decide, Take Action and Check Results), I thought about how difficult it can be to take unemotional approach to a situation where you are emotionally involved.
But, being effective in a supervisory role requires the ability to look beyond the emotions and focus on what is best for the organization. The importance of a supervisor is often overlooked but, he or she probably has one of the most difficult positions within a manufacturing plant. It is the supervisor’s responsibility to produce consistent results in order to meet the business objectives, however, they are also responsible for addressing the day to day concerns of the hourly employees. I imagine the supervisor being pulled in both directions when at times, these two groups are perceived to be diametrically opposed. The supervisor is expected to be calm under pressure, patient, demanding, understanding, unyielding, etc.
Have you looked at the organization through the supervisor’s glasses? Do they have the skills they need in order to keep your organization moving in the direction you want it to move? Are they getting the support they need in order to address the concerns of the hourly work force while focusing on the organizational goals?
For more practical tips for manufacturing professionals to attract, train and retain your hourly workforce, go to www.keyprocessinnovations.com.
by Julie | Apr 28, 2016 | Consulting, Efficiency, Employee Training, Interim Management, Management, Safety
TRAINING WITHIN INDUSTRY
Over the past few years, I have had the pleasure of being an instructor at the Investment Casting Institute’s Process Control Class. It was in this class that I had my first introduction to Training Within Industry.
During World War II, there was a shortage of skilled and trained workers at a time when the demand on manufacturing was very high. As a result, Training Within Industry was developed to quickly and efficiently train operators.
There are four programs of Training Within Industry:
- Job Instruction (JI) – this component teaches trainers how to train
- Job Methods (JM) – a methodology that employees use to make their job easier
- Job Relations (JR) – an analytical method for addressing personnel issues
- Program Development (PD) –how to solve production problems that are unique to a particular organization
Each of the programs are broken into four steps and the training and implementation of these programs is very structured. However, the organizations which followed this approach realized unbelievable results. After the war, TWI became less common place in the United States, however, the Japanese learned about it and TWI is credited to be the foundation of Lean Manufacturing.
In the book Training Within Industry by Donald Dinero, the author states that “TWI helped lay the bases for “learning organizations,” where successful companies train their employees to question, think and solve problems. “
Can you imagine a better workforce than one that can question, think and solve problems? There are a number of resources available online to learn more about Training Within Industry. In the upcoming articles, I’ll provide more information on each of the programs.
For more practical tips for manufacturing professionals to attract, train and retain your hourly workforce, go to www.keyprocessinnovations.com.
by Julie | Apr 14, 2016 | Consulting, Employee Training, Interim Management, Management, Onboarding, Safety
THE START OF SOMETHING BEAUTIFUL
Starting a new job can be a little stressful. Meeting new people, learning new tasks and an adjusting to a new workplace culture. Can you think back to your first day with your current employer? Were you nervous? Excited? How were you greeted by your new peers? Was everyone expecting you?
Some employers seem burned out from the hiring phase – it is like a revolving door for new employees. Employees are hired and then they leave within a week or two resulting in more time and money spent on recruiting and training.
Without a doubt, hiring employees has gotten much more difficult in recent years. There is a shortage of skilled workers who have the workplace competencies needed in manufacturing. So, recruiting qualified candidates is much more difficult. (Check out this article on tips on recruiting the most qualified employees.)
But, once you have selected a qualified employee, you want to make them feel welcome. Have you thought about the first impression you give your new employee on their first day? Could you do more to let your new employees know you view them as a valuable member of your team? Here are few suggestions that could help in retaining your new employees:
- Interview current employees about what they thought about their first day, week or month with the company. What was their impression of how they were welcomed by the company? What is one thing they would like to see improved or implemented?
- Establish a mentor program so veteran employees can assist new hires assimilate into the culture.
- Create an employee based committee to assist in developing and instituting the onboarding process. You might even consider allowing them to participate in interviewing candidates.
- Provide a checklist for the hiring manager or supervisor so they can ensure the company is prepared for a new employee prior to the first day.
Establishing an onboarding program is an important part of retaining your work force (check out this blog for more information on onboarding). But, don’t overlook the importance of making a good impression on the first day. Making the employee feel welcome and helping them adjust to your culture can help retain a valuable new employee.
For more practical tips for manufacturing professionals to attract, train and retain your hourly workforce, go to www.keyprocessinnovations.com.
by Julie | Apr 7, 2016 | Consulting, Employee Training, Interim Management, Management, Onboarding, Safety
The goal in manufacturing is to SAFELY make an end product that meets customer specifications with the lowest cost possible. There is nothing more important than the safety of the employees. But even looking beyond the employee, having a strong safety culture also impacts your bottom line.
I recently met with a manufacturing professional who shared if you want to know if a company is profitable, ask them about their safety statistics. If they don’t know them off the top of their head or can’t find them quickly, they are probably struggling financially. Without a strong safety program, eventually the number of workplace accidents will start to climb.
When thinking about workplace accidents, I imagine an iceberg with 20% above the water and 80% below the water. The cost of the accident is the part above the water including doctor/hospital bills, employee time-off, etc. But, the actual cost is what is under the water which includes increased insurance premiums, higher payroll and reduced plant productivity.
But, you don’t have to take my word for it. I found a lot of data that supports the relationship between a strong safety culture and profitability, including the following:
- A Liberty Mutual survey reports 61% of executives say $3 or more is saved for each $1 invested in work place safety (http://www.the-osha-advisor.com/CASE.html)
- Participation in OSHA’s Voluntary Protection Program saved one company $930,000 per year and the company had 450 fewer lost-time injuries than its industry average (http://www.asse.org/bosc-article-6/)
- According to the American Society of Safety Engineers, investment in health and safety programs can result in saving in workman’s comp claims, liability damages and litigation costs in addition to improvement in productivity and employee morale.
Providing a safe workplace for your employees is a win-win. It is good for the employees and good for your bottom line. If you believe your safety program needs a little work, there are a number of resources available online including an article I recently wrote on the importance of reporting near-misses.
For more practical tips for manufacturing professionals to attract, train and retain your hourly workforce, go to www.keyprocessinnovations.com.
by Julie | Mar 31, 2016 | Consulting, Efficiency, Employee Training, Interim Management, Management
WITH RIGIDITY OR FLEXIBILITY?
One of the reasons operators are trained to do a task the same way is to ensure uniformity and reduce process variability. However, this approach may not take into account how operators should react to slight process variations.
Yes, we want consistency from operator to operator but, we also want the operator to be aware of process fluctuations and adjust accordingly. One of the benefits of having an operator do a job rather than a robot is that they can observe the process. However, operators need to know what to do when slight changes are observed. Should they modify the process or stop production and notify management?
Some argue that operators should all do the same thing and not make any changes to the process. Others suggest that it is best to have operators aware of the overall process and the desired end result and then give them the flexibility to modify the steps based on their perceived best method. I see benefits and challenges with each of those approaches.
If operators are instructed to follow the process exactly as they were trained, the following questions come to mind:
- What is the impetus for making improvements to the process?
- What if a shift in the process impacts the final product?
- How do the operators provide input for a better method?
- Who decides whether this new method should be implemented?
If the operators have the flexibility to modify the process based on their perceived best method, I start to question:
- How do the operators know that their modification won’t impact product quality?
- Is their modification the most ergonomic method?
- Will other operators try the same modification but achieve a different result?
Regardless of the how you approach improvements to a process, it is critical that the operators have input. They work in the process on an ongoing basis and will detect subtle changes that might otherwise go unnoticed. Establishing a method for incorporating process improvements will go a long way towards reducing process variability.
For more practical tips for manufacturing professionals to attract, train and retain your hourly workforce, go to www.keyprocessinnovations.com.
by Julie | Mar 18, 2016 | Consulting, Employee Training, Management, Onboarding
Understanding the Learning Continuum
I don’t believe that any parent would allow a teenager to drive on a freeway without practice to develop the required skills. Learning to drive needs to be introduced in steps: first, a large parking lot, then maybe some side streets. Once that seems easy, start driving on some busier streets and then eventually head onto the freeway. Along the way, the driver exhibits understanding before progressing onto the next step. The final demonstration is a written and practical test at the local DMV.
Not all operator training needs to be as structured as learning to drive. But, we can agree that it takes time to learn the skills necessary to perform a task efficiently. And before moving onto the next task, the student needs to demonstrate a certain level of competency.
A Gordon Training International employee, Noel Burch introduced the “Four Stages for Learning Any New Skill” in the 1970s. These four stages are:
Stage 1: Unconsciously Incompetent – I don’t know what I don’t know
Stage 2: Consciously Incompetent – I know what I don’t know
Stage 3: Consciously Competent – I know what to do but still need to think about it
Stage 4: Unconsciously Competent – I know what to do it and don’t need to think about it
Unfortunately, many manufacturers label operators as trained or not trained. However, being aware of these four stages can help develop a Skills Matrix for your plant and your employees. Defining Stage 1 and Stage 4 is relatively easy, but, how do you define when an operator is at Stage 2 and 3? What is your criteria for determining when an operator moves from Stage 1 to Stage 2? How about from Stage 2 to Stage 3?
Adapting these four levels to a Skills Matrix for your employees could include the following criteria:
Stage 1: Minimal Understanding – must have constant supervision
Stage 2: Some Understanding – can work independently but supervisor must check work periodically
Stage 3: Fully Trained – can work independently
Stage 4: Trainer – able to train others how to do the task
Utilizing these 4 stages within your Skills Matrix can highlight areas and operators within your organization which would benefit from additional training. It can also be used as a tool during employee reviews.
As you look at your operator training program, where do you fall on the continuum? If you aren’t at level 4, what do you need to do in order to get there?
For more practical tips for manufacturing professionals to attract, train and retain your hourly workforce, go to www.keyprocessinnovations.com.
by Julie | Mar 10, 2016 | Consulting, Employee Training, Management, Onboarding
A number of years ago when I was a “wee little chick”, I was called into a room full of managers and told that I had been selected to attend a training. I wasn’t given any of the reasons behind the training, the goals for attending the training or the duration of the training. To be honest, I don’t exactly remember my frame of mind when I heard I had been selected, but, according to the trainer, my body language clearly conveyed that I was skeptical of the training and the trainer. Over the duration of the training, I learned a great deal about myself and how to be an effective manager and to this day, I also have the pleasure of calling that trainer my mentor.
This story is a good reminder that most people are skeptical about attending training. Questions that may run through their mind include: Why am I here? Is this really important? What are the motives of the management team in selecting me for this training?
When it comes to preparing your employees, it is critical to be aware of these concerns and if possible, take steps to alleviate those concerns prior to commencing. Communication is an important part of ensuring your employees get the most out of the training. This communication can include why the training is important to the employee, why it is important to the company and what the company wants to achieve by investing in the training.
In some instances, training is a precursor to changes that are going to be instituted at the company. And the employee concerns may be around those changes and how it will impact him. Acknowledge that and provide the opportunity for the employee to share his or her concerns.
After the training, take some time to get feedback on the training, what worked well and what could be improved. Not all training needs to be as entertaining as a U2 concert but, it is important that the employee gains the necessary skills, understanding or mindset in order to have the desired impact on the organization.
There is no doubt that if my manager had a 5-minute conversation with me about the training and why they were sending me prior to the initial meeting, I would have been much more receptive to what the trainer was sharing. Yes, over time I did find value in the training, but, being prepared ahead of time would have allowed me to learn even more. As you send your employees to training, I hope you will learn from my experience and prepare your employees in order to optimize their learning.
For more practical tips for manufacturing professionals to attract, train and retain your hourly workforce, go to www.keyprocessinnovations.com.
by Julie | Feb 25, 2016 | Consulting, Efficiency, Employee Training, Interim Management, Management
A lot of people claim to have a “6th Sense” when assessing a situation. But, when it comes to making a business investment, having a benchmark and being able to quantify improvements is essential. Making process improvements in your process may require an investment in financial, personnel or temporal resources and in order to justify the investment, you may need more than a sense in order to get the necessary support. 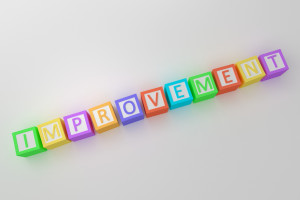
No matter what problem solving methodology used within your plant, most start by defining the problem. And part of this initial step includes identifying measures of process performance and establishing a baseline. An often overlooked reason for this step is to ensure the gains are sustained after improvements have been implemented.
Listed below are some metrics that can be used to measure process performance.
- First Pass Yield. This measures the number of good units produced against the total number of units produced. Depending on your process, this measurement can be broken down by department, by machine or by operator.
- Value Added vs Non-Value Added Time. Gathering data for this can be done via Value Stream Mapping or through Time Observations. From these studies, value and non-value added steps can be identified. As non-value added time is reduced, process output should increase.
- % Uptime. By defining % Uptime as outlined below, this measurement also takes into account set-up, changeovers, loading, unloading, idle time, breaks, cleaning, maintenance, etc.
% Uptime = (Value Added Time) x 100
(Operating Time)
- Process Capability, Cp or Cpk. In order for a process to be considered capable, it needs to be stable. Process stability means having consistent centering around the mean and predictable variation.
As you look towards making improvements in your process, try to pick a metric currently in use (or one that should be implemented) and use that to establish a baseline. Then utilize that metric to show areas which need improvement. Additionally after changes are made, data is available to document the improvement and provide a metric to sustain the gains.
For more practical tips for manufacturing professionals to attract, train and retain your hourly workforce, go to www.keyprocessinnovations.com.